Recesja związana z wybuchem pandemii koronawirusa mocno dała się we znaki polskim przedsiębiorcom. Wiele firm i zakładów przemysłowych postanowiło jednak wykorzystać czas spowolnienia gospodarczego a także koniec przestojów w produkcji na inwestowanie w najnowsze rozwiązania technologiczne.
Zdaniem ekspertów taktyka stawiania na innowacje może okazać się skuteczna w budowaniu rezerw kapitałowych do wykorzystywania ich w przyszłości na zrównoważony rozwój przedsiębiorstw, które staną się bardziej odporne na rynkowe wahania.
Pandemia koronawirusa całkowicie zmieniła plany inwestycyjne polskich przedsiębiorców. Z I edycji badania firm „KoronaBilans MŚP” przeprowadzonego na zlecenie Krajowego Rejestru Długów Biura Informacji Gospodarczej wynika, że ponad 54% właścicieli polskich firm w ciągu najbliższych trzech miesięcy zamierza wydać środki na zakup nowych sprzętów. Prawie 32% chce zainwestować w nowoczesne systemy IT i innowacyjne rozwiązania. Zarządzający krajowymi biznesami liczą, że przeznaczanie większych funduszy na idee i produkty z zakresu smart factory, wydatnie zmniejszy koszty i w dobie pracy zdalnej będzie szansą na odbudowanie rezerw kapitałowych. Wśród opcji jest też budowa i tworzenie nowych aplikacji, stron internetowych czy sklepów on-line. Eksperci szacują, że w ciągu 5 lat poziom automatyzacji w niektórych branżach polskiej gospodarki wzrośnie o połowę.

Epidemia nie zostawiła nam wyboru. Wymusiła wręcz na firmach transformację cyfrową i automatyzację wielu procesów. Jeśli więc ktoś do tej pory decyzje technologiczne odkładał na ostatnią chwilę, dziś musi je podjąć w ekspresowym tempie, ponosząc przy tym znacznie wyższe koszty. Przyspieszony kurs cyfryzacji stał się ważniejszy niż budowa i remont powierzchni biurowych, czy nawet zakup niektórych komponentów i materiałów do produkcji. Od niego bowiem teraz zależy nie tylko ciągłość działania przedsiębiorstwa, ale i przewaga konkurencyjna na rynku
Implementacja technologii
Według badania pod tytułem „Gotowość firm produkcyjnych do wdrożenia rozwiązań Przemysłu 4.0”, przeprowadzonego jeszcze przed wybuchem pandemii koronawirusa wśród 228 przedsiębiorstw, działających w czterech sektorach: maszyn i urządzeń, samochodów i sprzętu transportowego, mebli oraz wyrobów z metalu - największą motywacją do implementacji nowych technologii była chęć zwiększania wydajności produkcji. Taką odpowiedź wskazało 59% ankietowanych firm. Nieco mniej, bo 55% przedsiębiorstw za kluczową kwestię uznało obniżanie kosztów.
W opracowaniu „KoronaBilans MŚP” i w ujęciu sektorowym widać też, że w ciągu najbliższych trzech miesięcy, mimo rynkowych trudności, inwestować w rozwój planuje 16,7% firm produkcyjnych, 14,6% z branży budownictwa, 13,5% przedsiębiorców zajmujących się usługami oraz 4,2% z handlu. Optymizm panuje wśród średnich firm – tu fundusze na poprawę funkcjonowania wciąż ma do wydania 40% firm. Jednak sceptycznie do perspektyw rozwoju podchodzą już mali przedsiębiorcy – zaledwie 10% z nich będzie inwestowało w rozwój, jeszcze trudniejsza sytuacja jest wśród mikrofirm, ponieważ tu wskaźnik wynosi tylko 7%.
Koniec awarii
Profesjonaliści z branży na każdym kroku podkreślają, że dalsza automatyzacja, modernizacja, serwisowanie czy przeglądy sprzętu oraz weryfikacja poprawności funkcjonowania procesów produkcyjnych i sprzedażowych dadzą wymierne efekty po zakończeniu pandemii. Czas po przymusowych przestojach w produkcji należy jak najpełniej wykorzystywać na inwestycje w technologie i rozwój parku maszyn. To w długofalowej perspektywie zapewni skuteczne zarządzanie biznesem w czasie rzeczywistym i pozwoli natychmiast reagować na nieprzewidziane globalne wydarzenia.
W zautomatyzowanych zakładach produkcyjnych kluczową kwestią jest bezawaryjne i sprawne funkcjonowanie parku maszyn.
Zakończenie jednego procesu w szybkim terminie, warunkuje równie szybkie rozpoczęcie programowania kolejnego działania. Montaż specjalistycznych czujników wykrycia awarii czy systemów nadzorujących sprawną pracę, zarówno ludzi, jak i maszyn, nawet o kilka razy zwiększa możliwości produkcyjne i potęguje uelastycznienie wszystkich procesów fabrycznych –
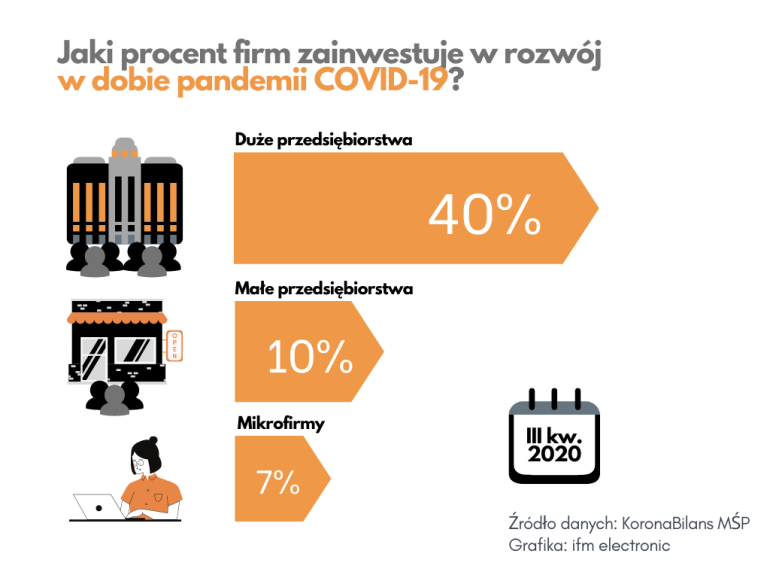
Przykładowo optymalizacja procesów czyszczenia jest możliwa dzięki systemowi monitorowania filtrów. Wydłużając cykle czyszczenia z tygodnia do kwartału, można uzyskać oszczędności rzędu 10 tysięcy euro na zaledwie jednej unikniętej operacji wymiany filtrów.
Konkurencyjne systemy
Stosowanie rozwiązań smart factory, między innymi w postaci ultranowoczesnych czujników temperatury, ciśnienia, drgań, poziomu, przewodności oraz systemów z zakresu monitorowania czy okablowania, w powiązaniu ze współczesną automatyką przemysłową, spełni najwyższe wymagania w wielu fazach produkcji i zapewni dotrzymanie kroku konkurentom w technologicznym wyścigu. Powiązane ze sobą systemy czujników mogą diagnozować pracę maszyn i całych linii produkcyjnych, przekazując nawet najmniejsze odchylenia parametrów, chroniąc przed kosztowną awarią urządzeń.
Kolejne niezaplanowane przestoje będą generować dodatkowe koszty i straty, które mogą wiązać się ze wstrzymaniem całego procesu ciągłości produkcji lub skomplikowaną naprawą maszyn, czasem nawet karami za niedotrzymanie umownych terminów. Unifikacja systemowego działania fabryk, zwłaszcza w dobie pandemii, zwiększa wydajność na wszystkich etapach powstawania konkretnych produktów. Począwszy od składania zamówień, dostarczania komponentów przez produkcję, wysyłkę gotowego towaru, aż do obsługi posprzedażowej - zdalnej, internetowej lub telefonicznej.
Praca na przyszłość
Specjaliści wskazują również, że wykorzystywanie rozwiązań Przemysłu 4.0. pozwala nowoczesnym przedsiębiorstwom produkcyjnym lepiej zabezpieczać się na wypadek niedoboru pracowników i ograniczonych zasobów kadrowych, spowodowanych na przykład przymusową kwarantanną.
Według ostatnich danych Głównego Urzędu Statystycznego w maju produkcja sprzedana polskiego przemysłu była niższa o 17% w porównaniu z majem 2019 roku, gdy zanotowano wzrost o 7,7%. Ze względu na spowolnienie gospodarcze spowodowane pandemią koronawirusa w ujęciu narastającym rok do roku w okresie styczeń-maj tegoroczna produkcja spadła o 7,9%. Po wyeliminowaniu wpływu czynników o charakterze sezonowym, w maju produkcja sprzedana przemysłu kształtowała się na poziomie o 15,5% niższym niż w analogicznym miesiącu ubiegłego roku.
Ostrożne, ale optymistyczne warianty Ministerstwa Rozwoju sygnalizują już jednak, że w czerwcu straty mogą zostać częściowo odrobione do poziomu o 5% niższego niż w czerwcu ubiegłego roku. Przedstawiciele branży przemysłowej podkreślają, że to pośredni efekt wykorzystywania rozwiązań smart factory na coraz większą skalę. Innowacyjne systemy monitorowania produkcji czy specjalistyczne rozwiązania dostosowane do zmiennej rzeczywistości bezpośrednio przekładają się bowiem na powrót do generowania oszczędności, a wypracowane w ten sposób rezerwy kapitałowe można ponownie przeznaczać na inwestycje w dalszy rozwój, zarówno technologiczny jak i kadrowy.